8 July 2025
Ah, the smell of fresh concrete, the symphony of power tools, and the thrill of watching a slab of land become someone’s dream home… until the invoice for lumber arrives and it looks more like a luxury sports car price tag than a stack of 2x4s.
Welcome to the wild world of new construction in 2024, where building materials are doing their best impression of Bitcoin—volatile, expensive, and making builders everywhere break into a nervous sweat.
But don’t panic! Builders aren’t just sitting around hoping prices come down while brushing sawdust off their blueprints. Nope, they’re rolling up their sleeves, getting creative, and finding clever ways to outwit the chaos caused by rising material costs.
So grab your hard hat and hammer (or at least a cup of coffee), and let’s dig into how builders are tackling this wallet-tightening problem with some savvy strategies—and maybe a little elbow grease.
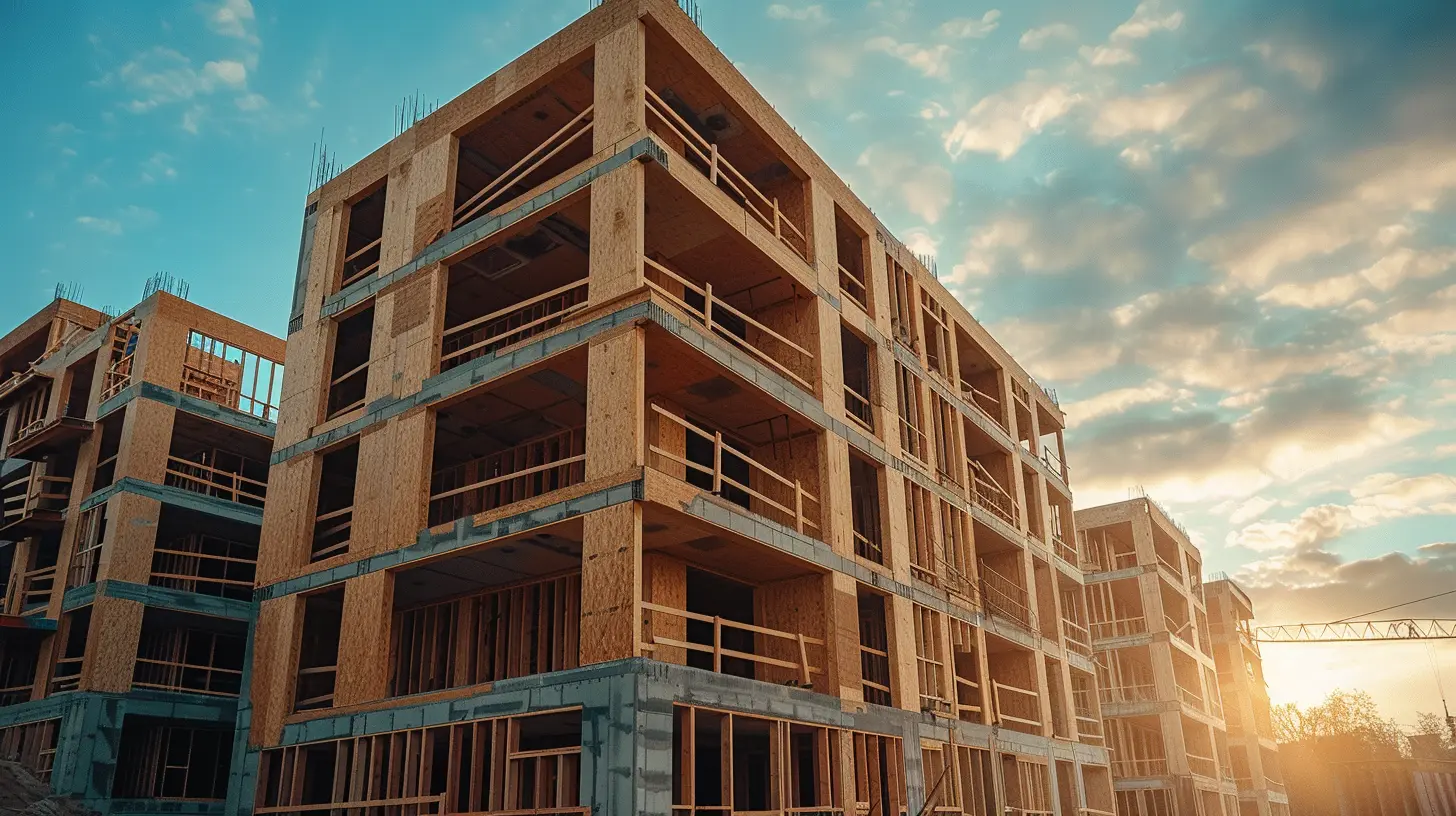
The Pricey Elephant in the Room: Why Are Material Costs Through the (Metaphorical) Roof?
Before we dive into the solutions, let’s address the elephant in the lumber yard.
Over the past few years, material prices have become the wild child of the construction world. Lumber? Up. Concrete? Up. Steel? You guessed it—also up. And remember when drywall was boring? Not anymore. Even that’s gotten a little too full of itself lately.
There are a few culprits behind this:
- Supply chain disruptions (we’re looking at you, global pandemics and shipping delays)
- Labor shortages (everyone seems to have ghosted the construction industry)
- Raw material scarcity (trees don’t grow overnight, unfortunately)
- Inflation (because, of course)
So, yeah, builders have been handed a complicated blueprint, but they’re not backing down from the challenge.
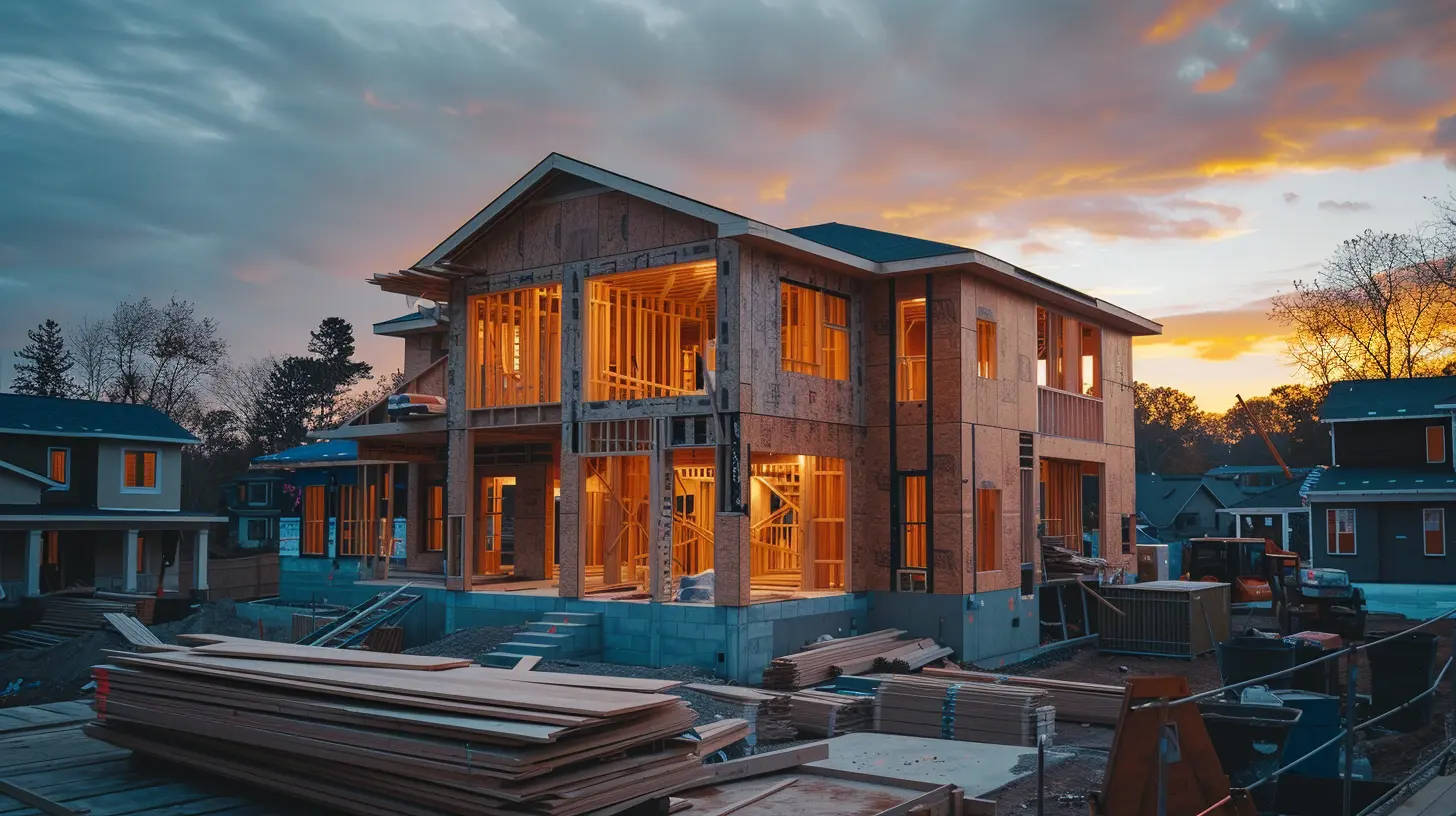
1. Getting Smart with Design: Do More With Less
One of the first things builders are doing?
Rethinking design. Because sometimes less really is more (except when it comes to cheese on nachos—always more there).
Open Floor Plans for the Win
Open floor plans are not just stylish—they also require
less framing material and drywall, which equals fewer costs. Think of it as a win-win: homeowners get a Pinterest-worthy layout, and builders get to save on materials.
Modular and Prefab Construction
No, prefab homes are not the sad, cookie-cutter boxes you might be picturing. Modern modular construction is like the IKEA of homebuilding (minus the 4-hour assembly instructions and missing screws). These builds use factory-assembled parts that save both time and materials, allowing for bulk ordering and less waste. Efficiency is the name of the game.
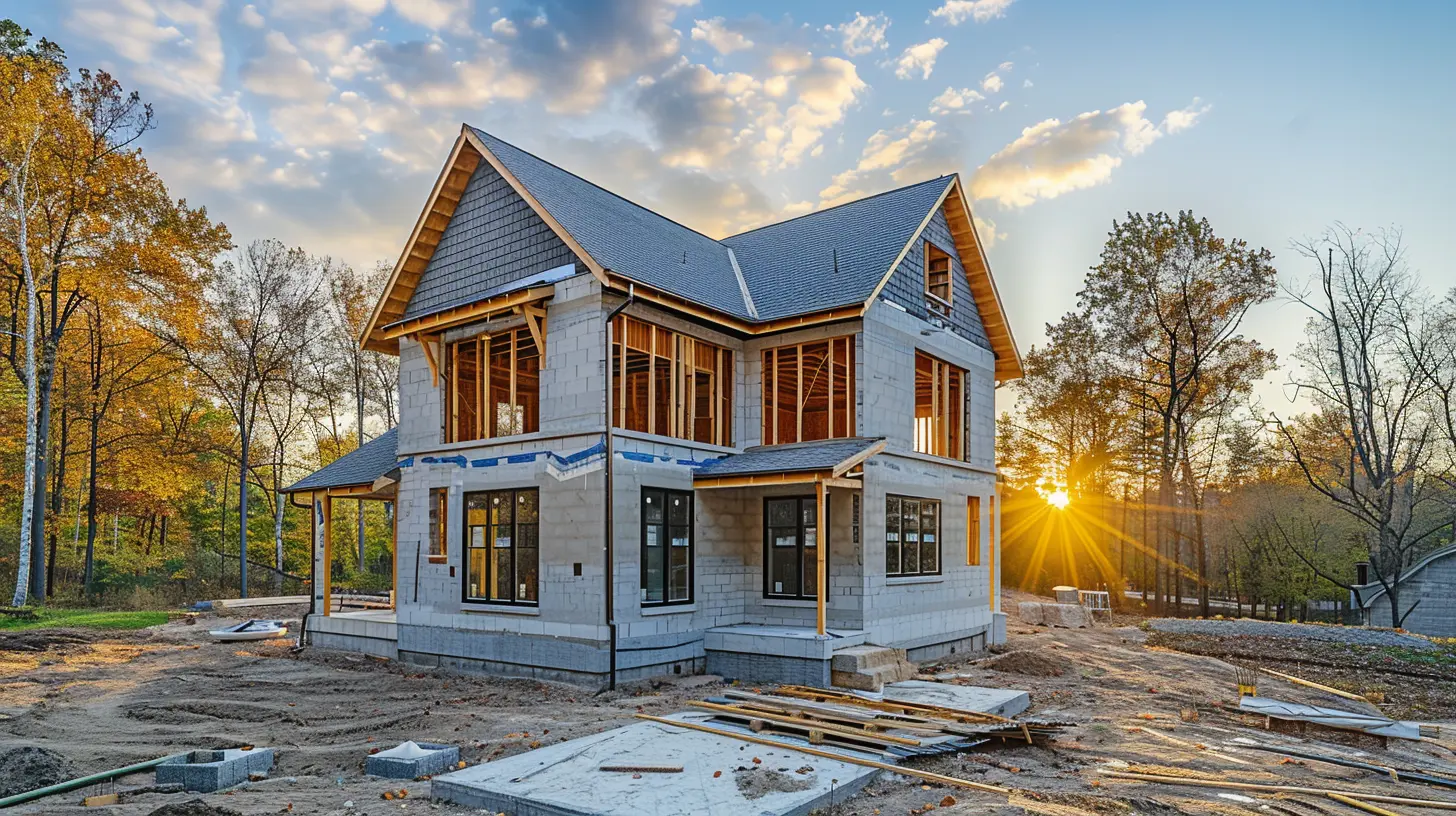
2. Buying Smarter: Bulk Orders, Alternative Materials, and Playing the Supplier Field
If builders were dating the material world, they’d be actively swiping right on better deals. Here’s how they’re getting strategic:
Bulk is Beautiful
Builders are pooling resources with other companies to make
bulk purchases of lumber, concrete, and steel—because let’s face it, everything’s cheaper when you buy enough for a mini city.
Playing the Supplier Field
Loyalty is great in relationships, but when it comes to materials, it’s okay to shop around. Builders are working with
multiple suppliers to compare prices, hedge against shortages, and avoid putting all their bricks in one basket.
Substituting Like a Top Chef
Builders are also channeling their inner Gordon Ramsay—substituting ingredients without compromising quality. Instead of rare and expensive wood types, they’re using
engineered wood, bamboo, or reclaimed materials. Concrete alternatives like
hempcrete and even
recycled plastic insulation are showing up on construction sites nowadays. Who knew building a house could be so eco-fabulous?
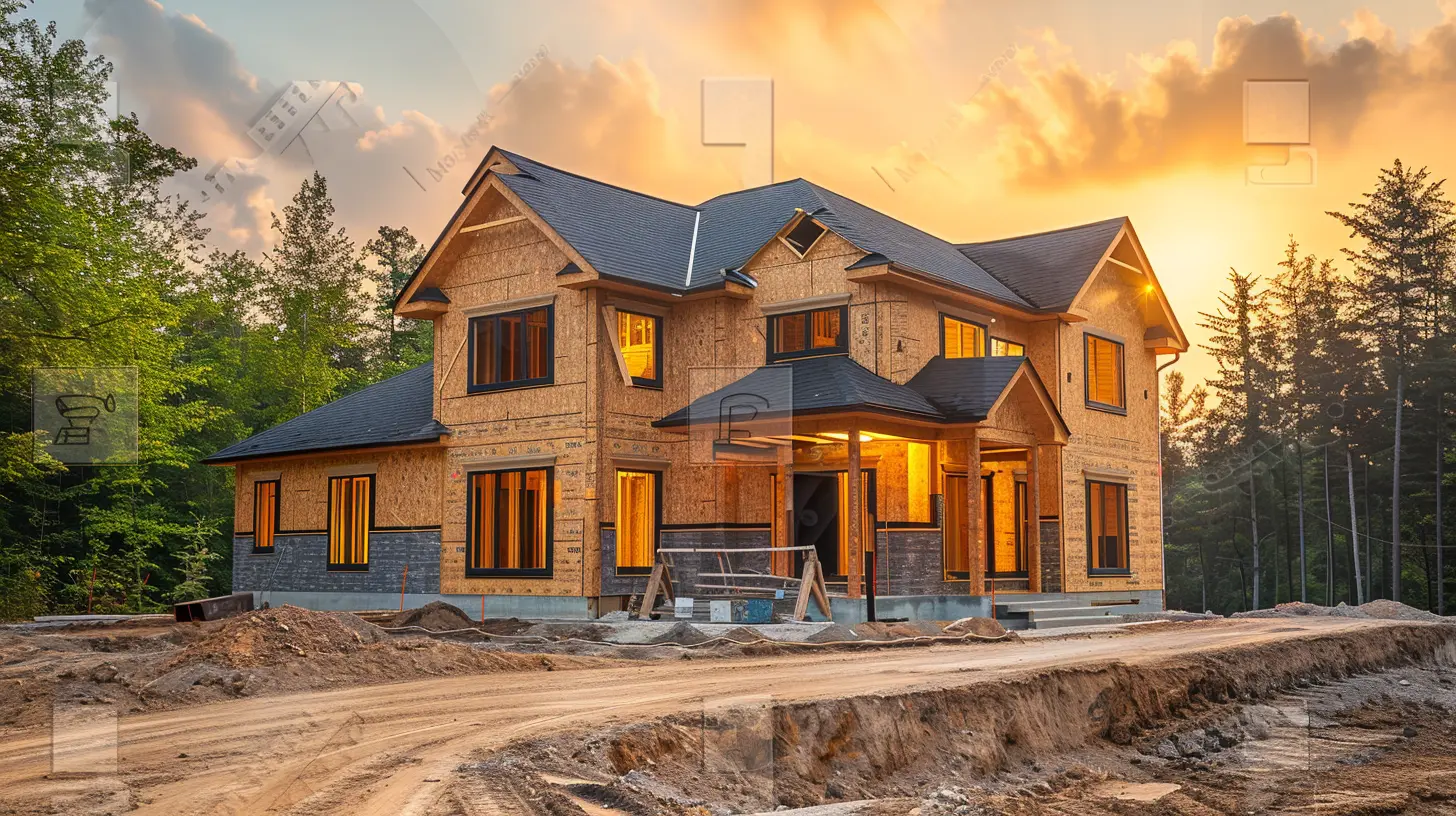
3. Technology: The Construction Site's Secret Weapon
Gone are the days when building a home meant just a hammer and nails (and probably a thrown-in swear word or two). Today, technology is strapping on its tool belt and helping builders fight rising material costs like a superhero with a nail gun.
3D Modeling and BIM (Building Information Modeling)
Builders are using 3D models to virtually construct a project before even a single brick is laid. It’s like playing Sims—but way more expensive. This helps identify material waste, clashes in design, and opportunities to optimize.
Project Management Software
Spreadsheets are out; fancy dashboards are in. With tools that
track inventory, budget, and supplier timelines, builders are staying ahead of delays, preventing double orders, and cutting down on waste. It’s like having a very organized construction fairy godmother.
Drones for Site Inspections
Yes, drones. Because nothing screams “modern construction” like a tiny helicopter zipping through your job site. Drones help monitor progress, track materials, and ensure everything’s going according to plan—without burning fuel or time.
4. Recycling: One Builder’s Trash is Another Builder’s Treasure
Builders are embracing the power of reuse. We’re not saying they’re dumpster diving, but let’s just say they’re giving older materials a comeback worthy of a ‘90s fashion trend.
Salvaged Wood and Fixtures
Think vintage, but make it structural. Builders are reclaiming wood from old barns, beams, and even bleachers (imagine cheering on your home’s past life!). These materials add character
and save money.
Recycling On-Site Waste
Instead of tossing off-cuts and excess materials, builders are increasingly
crushing, melting, or reshaping them for use in other parts of the job. Efficient, sustainable, and kind of like construction’s version of composting.
5. Lean Construction: Cutting the Fat Without Cutting Corners
Lean construction isn’t about builders going on diets (though we hear caffeine consumption is at an all-time high). It’s a strategy focused on
eliminating waste and improving flow throughout the project.
Scheduling Like a Pro
Builders are now
scheduling trades and deliveries with military-level precision. No more having the electrician show up three weeks before the wiring arrives.
Just-In-Time Delivery
Much like your Amazon Prime package, materials are now arriving
exactly when needed—not a second too soon or too late. This tactic reduces on-site clutter and the risk of damage or theft (because, let’s face it, stacks of unused lumber are tempting for the five-finger-discount types).
6. Transparent Pricing and Client Communication
Here’s where builders are swapping out their hard hats for therapist hats. Rising costs can freak out homebuyers, and nobody wants a meltdown over the price of drywall.
Clear Contracts with Material Escalation Clauses
Builders now include
material escalation clauses in their contracts. Think of it as a construction prenup—it outlines what happens if prices spike, so both parties are protected and there are no surprises (except maybe the color of the kitchen tile).
Frequent Updates and Cost Breakdowns
Builders are keeping clients in the loop with
regular budget updates, showing exactly where costs are coming from. Transparency goes a long way when you’re shelling out six figures, right?
7. Going Green to Save Green
Eco-friendly building methods aren’t just good for the planet—they’re also becoming surprisingly cost-efficient.
Energy-Efficient Materials
Smart insulation, low-E windows, and solar-ready roofs might cost a
little more upfront, but they reduce long-term operating costs and can even qualify for rebates. Builders promoting these features are
future-proofing homes and wallets.
Sustainable Sourcing
Certifications like
FSC (Forest Stewardship Council) tell buyers that their wood didn’t come from some illegal lumber-ring deep in an endangered rainforest. Buyers love it, and builders can often receive incentives for sourcing responsibly.
8. Training and Retaining Skilled Labor
A sharp crew can actually help reduce material waste (and headaches). Builders are putting extra effort into:
- Training workers on efficient material use
- Retaining experienced crew members who know how to “measure twice, cut once”
- Cross-training staff so work doesn't stall while waiting for that one specialist to show up
Better labor, fewer mistakes, and less waste? That’s a three-for-one deal if there ever was one.
So, Is It All Doom and Gloom?
Not at all. Sure, material costs are high, but builders are proving they can roll with (and around) the punches. With smart strategies, better tools, and a little imaginative elbow grease, they’re still helping people build their dream homes—without dreaming of bankruptcy.
And hey, at least no one’s building with literal sticks and stones anymore, right?
Final Thoughts: The Future is Built on Brains and Balance Sheets
Builders today are part artist, part economist, and part superhero. They’re juggling spiraling costs, demanding timelines, and sky-high expectations—and still managing to raise the roofs (literally and figuratively).
So next time you see a new home popping up on your block, give a little tip of your hard hat. Behind that build is a team navigating a maze of cost hikes with grit, grace, and maybe a few strong cups of coffee.